Securing and Standardizing Robotic Equipment
Discover how Alps Group helped Cartier standardize its robotic equipment, ensuring compliance with industrial safety requirements and European production standards.
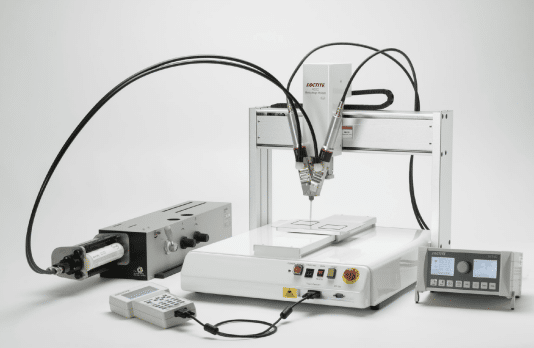
Context
Founded in 1847 in Paris by jeweler Louis-François Cartier, the Cartier House has become a global reference in jewelry, particularly with European royal courts. Since the early 20th century, Cartier has continued to innovate while preserving its exceptional heritage. Recently, to secure its production processes and comply with strict regulations, Cartier sought the expertise of Alps Group.
Bring Robots 200 and 400 up to compliance
Ensuring full conformity with the Machinery & OMach directives, meeting industrial safety standards, and ensuring uninterrupted production within European standards.
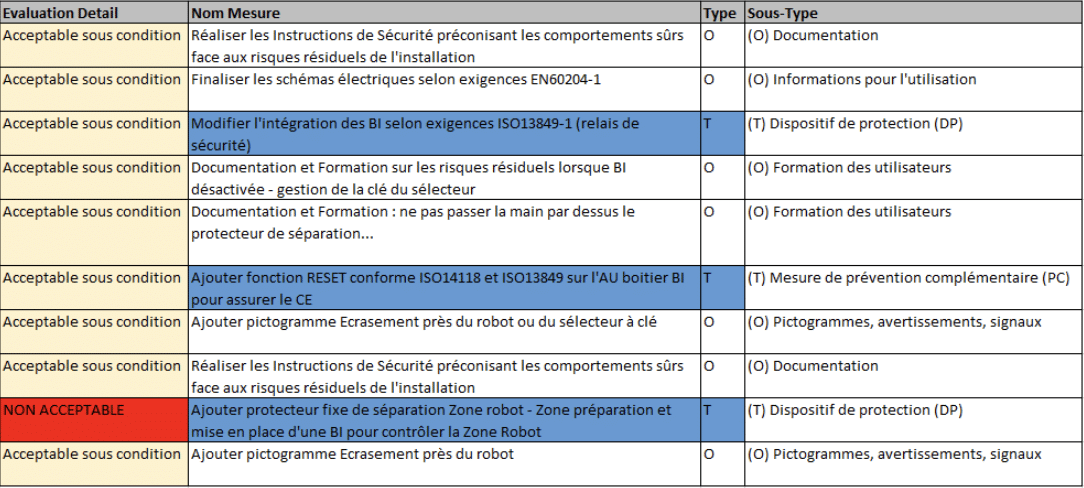
Achievements
Alps Safety, the division of Alps Group specializing in industrial safety, implemented several actions to secure and standardize Cartier’s robotic equipment:
- Installed a safety relay, a SICK immaterial barrier, and a RESET function command box in compliance with ISO13849-1 and ISO14118 standards
- Installed fixed protectors to separate the preparation area from the robotic zone
- On-site assembly and wiring, followed by the creation of electrical schematics in line with EN60204-1
- Issued a CE certificate signed by “ALPS Safety,” ensuring equipment compliance, along with detailed safety documentation for the user
This compliance now allows Cartier to meet European standards without compromising production flow.